- Recep Koca
- Eylül 5, 2020
- 19:46
- Yorum Yok
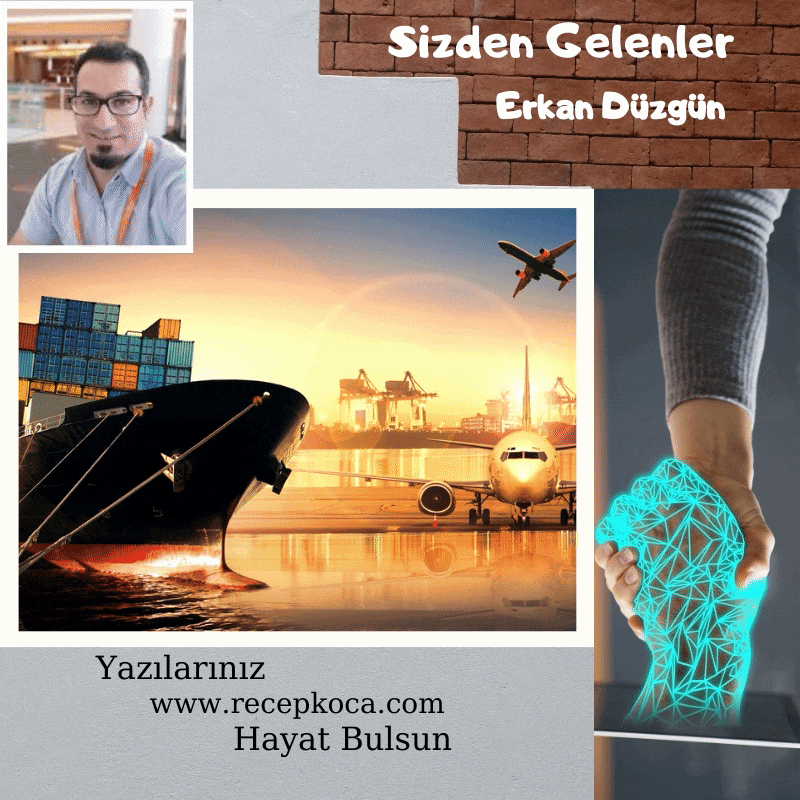
Lojistik Sektöründe Depoların Önemi
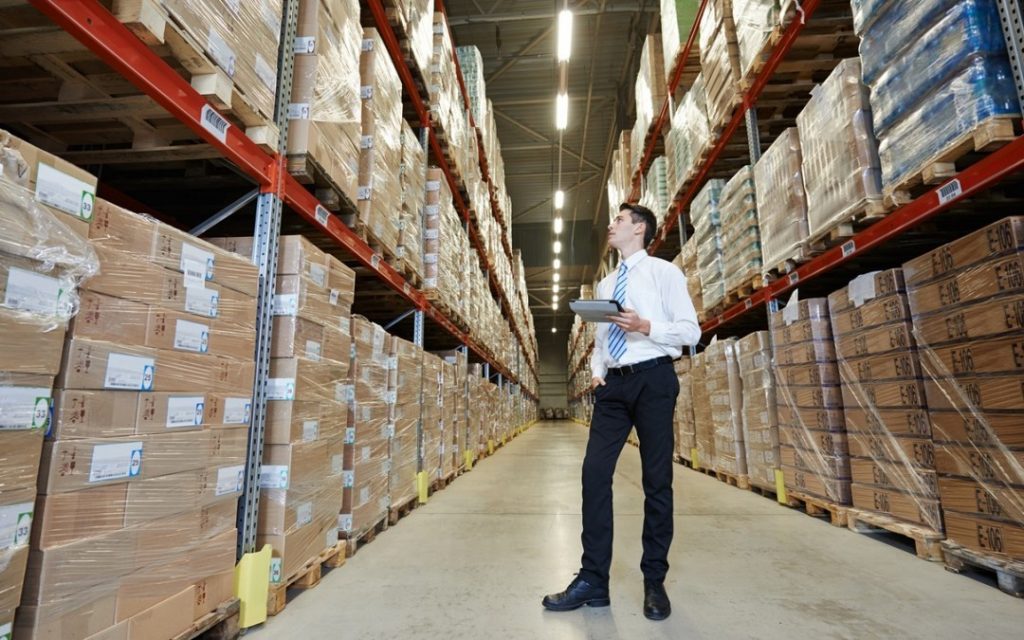
Depo, ürünlerin ham madde aşamasından üretim ortamına, oradan da tüketim merkezlerine, dağıtımına kadar olan bütün bir faaliyet dizisinin gerçekleştirilmesinde stratejik rol oynayan ara noktalardır. Lojistik sektöründe depoların çok önemli bir yeri vardir ve tüm işletmeler küçük de olsa bir depoya sahiptirler. Peki depolara yeteri kadar önem veriliyor ve tam anlamıyla doğru bir şekilde kullanılıyor mu?
Depolamanın, mal üreten, ithal eden, ihraç eden veya taşıyan çoğu işletme için bir gereklilik olduğunu söylemek yerinde olur. Bunu gereksiz bir masraf olarak gören işletmeler olduğunu söylemek de mümkün, fakat özellikle paradan tasarruf etmek ve üretkenliği en üst seviyeye çikarmak icin depolar isletmelerin olmazsa olmazıdır diyebiliriz.
Müşterinin vermiş olduğu bir siparişi teslim ettikten sonra da olay devam eder. Özellikle günümüzde rekabetin artması ve teknolojinin çok hızlı bir şekilde hayatımıza girmesi ürünü teslim ettikten sonraki süreçlere de odaklanmamız konusunda önemli bir etki oluşturmuştur. Tamda bu noktada depo envanterinin önemini görebiliriz. Depo envanteri üzerinde doğru ve daha etkili kontrol sağlayan firmalar müşterilerinin ürünlerini daha hızlı bir şekilde teslim eder ve kusursuz bir süreç yönetimiyle devamlılık sağlayıp karlarını daha hızlı bir şekilde arttırabilirler.
Detaylı bir şekilde araştırdığımızda küçük işletmelerin yaklaşık yüzde 24’ünün envanterinin olmadığını ve yaklaşık yüzde 8’inin ise envanterlerini takip etmediğini görebiliriz. Bu durum genellikle geç gönderilere, gecikmeli sipariş işleme ve kötü müşteri deneyimine yol açmaktadir.
Doğru bir şekilde yönettiğiniz depolarda mallarınız için merkezi bir konum sağlayarak envanterinizi daha iyi bir şekilde takip edebilirsiniz. Bir depoya yatırım yaparak ürünleri daha verimli bir şekilde depolar, gönderir ve dağıtırsınız. Bir ürün stokta kalmadıysa, bunu doğru envanter yönetimiyle hemen farkeder ve müşterilerinizi günlerce veya haftalarca bekletmek yerine daha alternatif seçenekler sunabilirsiniz.
Şirketlerin daha iyi depo envanter yönetimi ile verimlilik, maliyet ve zaman açısından depolarını en iyi şekilde kontrol edebilmeleri için belirli kurallarin yerine getirilmesi gerekmektedir.
Kural 1: Depo Tasarımı
Depolar için en önemli noktalardan biri de depo tasarımıdır. Doğru tasarlanmış depolarda riskleri en aza indirebilir ve çeşitli olağanüstü durumlarda önceden önlem alarak zararların önüne geçilebilir. Depo tasarımlarıyla ilgili pek çok riskli konunun olduğunu da unutmamak gerekir. Bunların en önemlileri arasında yangın, can kaybı ya da yaralanmalara yol açabilecek iş kazaları, bina taşınmazında ya da raf sistemlerinde yaşanacak çökmeler sayılabilir. Ancak tüm bu tehlikelerin aynı anda yaşanabileceği bir doğal afet olan depremle de her zaman karşı karşıya kalabiliriz.
Depo tasarımlarında deprem riskine karşi önlemler alınmalıdır. Sprinkler patlamaları ve raf sistemlerinin çökmesi veya kolilerin yanlış bir şekilde istiflenmesi gibi durumlar deprem anında can kayıplarına neden olabilmektedir. Bunların en iyi şekilde kontrol edilmesi ve düzenlenmesi gerekir. Ayrıca depo rafları depolarda iş kaybını azaltmak, işleyişi hızlandırmak, çalışma verimini artırmak ve ileriye yönelik büyümeyi kolaylaştırma görevlerinde de önemli bir rol almaktadır. Depo raf sistemi sadece stratejik açıdan değil, maliyet olarak değerlendirme yapıldığında avantajını daha çok ön plana çıkarmaktadır.
Öte yandan depolarda alınması gereken birkaç tedbiri sıralayacak olursak;
- Depolar 180 dakika aleve dayanıklı duman tahliye fanları, alarm kabloları ve alev yürütmez halojenden arındırılmış kablolamaya sahip olmalıdır.
- Depo içerisinde çalışan personelin deprem esnasında toplanacağı güvenlik alanları belirlenmelidir. Raflardan uzak, elleçleme, sipariş hazırlama ve sevkiyat alanları bunun için kullanılabilir. Çalışanların sarsıntı geçene kadar bu bölgelerde kalması sağlanmalıdır.
- Sarsıntı durduğunda dışarı çıkan personelin toplanacağı noktalar belirlenmelidir. Dışarı çıkma akışını engellememesi için tüm turnike ve kapıların kolayca serbest geçiş haline getirilebileceği bir düzenek kurulmalıdır.
- Raflar aşırı yüklenmemeli ve konroller sürekli yapılmalıdır.
- Palet ağırlıkları kontrol edilmeli, beyan edilen ağırlık ile paletin gerçek ağırlığının aynı olduğundan emin olunmalıdır.
- Raf sistemlerinde deprem çaprazlarının olduğundan emin olunmalıdır. Rafların arkasındaki çaprazların bir kısmı deprem çaprazı değil, palet yükleme esnasında hareket olmaması için kullanılan gergi elemanlarıdır. Asıl deprem çaprazları raflar gibi zeminde biter ve yere sabitlenmiştir. Bu şekilde deprem kuvvetini sönümleyerek zemine aktarırlar.
- Sprinkler sistemler için sismik askılama sistemleri kullanılmalıdır. Bu sayede hem olası bir alev anında sistemlerin sorunsuz bir şekilde çalışması güvence altına alınmış olunur, hem de zamansız patlayan sprinkler nedeniyle ürünlerin zarar görmesinin önüne önüne geçilebilir.
Depoların daha verimli kullanilabilmesi için ürünlerin doğru bir şekilde yerleştirilmesi gerekir. İlk giren ilk çıkar kuralı benimsenmeli sevkiyat içinde gerekli alanlar yeteri derecede olmalıdır.
Sürekliliği olan ürünler daima sevkiyatın olacağı lokasyonlara yakın olmalıdır. Talebin az olduğu ürünler daha geri planda tutularak depoda daha verimli bir ürün toplama süreci ve lokasyonların daha verimli bir şekilde kullanılması sağlanabilir.
Unutmamalı ki depoda yanlış lokasyonlara yerleştirilmiş ürünler birçok zararı beraberinde getirir ve sorunu çözmek için zaman, çaba ve para israfı ortaya çıkabilir. Ayrıca yanlış paketlenmiş ve yanlış toplanmış siparişler veya depoda kaybolmuş ürünler müşteri şikayetlerini de beraberinde getirerek şirket prestijinide ciddi bir şekilde olumsuz etkiler.
Depo koridor genişlikleri de doğru ayarlanarak ve depoda kullanılan makinelerin rahat hareket etmesi sağlanarak zamandan tasarruf edilebilir.
Kural 2: Çalışan Eğitimi
İnsan hatası, bir depo envanter yönetim sistemindeki hataların en yaygın nedenlerinden biridir. Bu hatayı azaltmanın anahtarı, çalışanlara doğru zamanda ve doğru eğitimin verilmesiyle sağlanabilir.
Çalışanların yetkinliklerine göre görevler verilip bu görevlerin yerine getirilmesinde moral desteği verilebilir gerekirse çeşitli ödüllendirme sistemleri ile de verimlilik en üst seviyeye çıkarılabilir.
Mavi yaka ve beyaz yaka arasında pek ayrım yapılmamalı ve personele her zaman şirket için ne kadar önemli olduklari anlatılmalıdır. Depolardaki en önemli unsurun çalışan değerleri olduğu unutulmamalıdır. Verilen cezalarla personeli işten sogutmak yerine daha yapıcı ve personele işi sevdirecek bakış açılarıyla hareket edilmelidir.
Görev dağılımları yapılırken personel doğru bir şekilde takip edilmedir. Deprem ve yangın esnasında sorumluluk alması gereken çalışanlar belirlenmeli ve bu çalışanların görevlerini tam olarak bildiğinden emin olunmalıdır.
Tüm personele deprem ve yangın esnasında ve sonrasında yapılması gerekenlerle ilgili eğitimler verilmeli ve belirli periyotlarda deprem tatbikatı yapılmalıdır.
Kural 3: Emniyet
Gerekli önlemler alınmadığında depolar tehlikeli bir çalışma ortamı haline gelir. Sahip olabileceğiniz her tip ve ölçekli depoda tehlikeler vardır ve bunlar arasında düşen stok, kullanılan makine veya araçlar ve yangın sayılabilir.
Bir depo çalışanının kazası sadece çalışan için kişisel bir durum değil, aynı zamanda sorumlu olan işverenin itibarı içinde büyük risktir. Daha da önemlisi, dava, zarar ve artan sigorta primleri de işletme için finansal bir risk oluşturur.
İyi bir depo yönetiminde etkin güvenlik önlemleri alınarak, riskler kapsamlı bir şekilde değerlendirilebilir ve bunların önüne geçilebilir. Örnek verecek olursak koruyucu ekipmanlar kullanılarak daha güvenli hale getirilebilir.
Kural 4 : Toplama Lokasyonları
Yukarıda da bahsettiğim gibi depolarda toplama lokasyonları her acçıdan daha hızlı ve doğru ürün sevkiyatlarının gerçekleşmesini sağlar. Toplama lokasyonlarının yeteri büyüklükte olması ve ürünlerin bu lokasyonlarda ayrı ayrı toplanması sağlanmalıdır. Ürünler toplanırken birbirine karıştırılmamalıdır. Bunun için her bir stok kalemi veya SKU (Stock Keeping Unit) için belirli yerler oluşturulmalıdır. Yanlış toplama kontrolde ve sevkiyatta zincirleme hata oluşturarak iş hacmini iki katına çıkarabilir ve her anlamda verimliliği düşürebilir.
Ürünlerin yerleri belirlenirken şu maddeler göz önünde bulundurulabilir:
- Ürünün hızına göre raf konumu belirlenmeli. (sipariş sıklığına göre toplama lokasyonlarına yakın bir yerde olabilir.)
- Yüksek hacimli SKU’lar için birden fazla toplama lokasyonları belirlenebilir.
- İlk giren ilk çıkar kuralına uyulmalı.
- Personel arasında iletişim kopukluluğunun önüne geçilmeli.
- Öncelikli ürünler rampalara yakın olmalı.
- Özellikle soğuk zincir olan sevkiyatlar önceden belirlenerek planlama yapılmalı.
- Toplama verimliliği ve doğruluğunu sağlamak için periyodik incelemeler yapılmalıdır.
Kural 5: Etiketleme
Etiketleme depodaki ürünlerin tanınırlığı için son derece önemlidir. Ürün depoya alınır alınmaz etiketlenmeli ve daha sonra gerekli lokasyonlara yerleştirilmelidir.
Etiketleme depo envanteri kontolü ve yönetimi açısından en önemli etkendir. Etiketleme ile ürünün ne zaman depoya geldiği hangi lokasyonda olduğu gibi tüm bilgilerinin kayıt altına alınması ve bunun takibinin kolaylaşmasıdır.
Doğru etiketler ile ürüne ulaşılabilirlik arttırılarak daha verimli ve hızlı bir sevkiyat süreci gerçekleştirilebilir.
Kural 6: Stok Sayımı
Stok sayımı, depolarda tutulan ürünlerin fiziksel sayımı ve doğrulamasıdır. Stok sayımı sıklığı işletmeden işletmeye değişiklik gösterir, bazı işletmeler yılda bir veya iki kez sayım tercih ederken, bazıları üç aylık veya aylık olmak üzere daha sık sayımlar tercih edebilmektedirler.
Stok sayımları ile envanter daha iyi bir şekilde takip edilebilir ve ürün hareketliliği de somut bir şekilde göz önüne alınarak gerekli önlemlerin alınması sağlanabilir. Sayımda dikkat edilecek konular, her kategori için farklı olmaktadır. Ürünlerin ambalaj özellikleri, sergilenme özellikleri, satış süreçleri, satış hızı gibi birçok etken, sayımda yapılması gerekenleri farklılaştırabilmektedir.
Stok ve Sayım Farklılıklarının başlıca nedenlerını sıralayacak olursak, bunlar:
- Eksik belgeler, yanlış ürün/adet girişleri,
- Yanlış ürün okutmaları,
- Sayımın yanlış yapılması,
- Barkodlamaki yanlışlıklar,
- Koli/adet tanım yanlışlıkları,
- İade ürünlerinin işlenmemesi,
- Bozuk/kırılan ürünlerin girilmemesi,
- Depolar arası sevkiyatların işlenmemesi,
- Şirket içi kullanımın kayda alınmaması,
- Mağazalar ve depolar arası sevkiyatlarda karşılıklı kontrol yapılmaması, adet anlaşmazlıkları,
- Bantlı promosyon ürünlerin, paketli alınıp tek tek satılması,
- Belge sevk tarihleri ve işlem tarihlerinin doğru girilmemesi,
- Ürünlerin çalınma riski, olarak sayılabilir.
Stok sayımları ile hangi ürünlerin sattığını ve hangilerinin satmadığını da görmemiz açısından önemlidir. Uzun süre raflarda bekleyen ürünler iade edilebilir veya farklı ürünlerle değiştirilerek maliyet azaltılabilir. Doğru va zamanında yapılan stok sayımları herzaman depolar için büyük avantaj olup gerektiğinde bu konu ile ilgili danışmanlık şirketlerinden de destek alınarak personele gerekli ibilgilendirme verilebilir ve bu şekilde stok sayımları en sağlıklı şekilde yapılarak envanter verimliliği maximize edilebilir.
Zamanında yapılmayan stok sayımlarının ileriki dönemlerde çok fazla masrafa ve depo verimsizliğine yol açacağı unutulmamalıdır.
Kural 7 : 5S Kuralı
5S kuralı, kaliteli bir çalışma ortamı oluşturmak ve bu ortamın sürekliliğini sağlamak için geliştirilen bir tekniktir. Çalışma koşullarını performans, konfor, güvenlik ve temizlik açılarından en iyi hale getirme amacı taşıyan bu teknik ülkemizde 5S tertip düzen sistemi olarak anılmaktadır fakat tam karşılığı 5S işyeri organizasyonudur.
5S sistemi, sadece tertip ve düzenden fazlasını amaçlamakta, işyerini veya yaşam alanlarını daha ergonomik, güvenli ve verimli hale amacı taşıyan bir sistemdir.
5S kuralı, 1950’lerde Japonya’da ortaya çıkmış olmakla birlikte Japonca Seiri, Seiton, Seiso, Seiketsu, Shitsuke kelimelerinin slogan haline getirilmiş halidir. Bu kelimeler sırasıyla Ayıklama, Düzen, Temizlik, Standartlaştırma ve Disiplin anlamlarına gelmektedir. 5S tekniği, endüstriyel üretimde yalın üretim metodunun vazgeçilmez bir adımı haline gelmiştir.
5S Kuralı Uygulama Adımları
· Ayıklama (Seiri)
Çalışma alanında sürekli olarak ihtiyaç duyulmayan malzeme, ekipman ve aletlerin düzenli bir şekilde çalışma alanından uzaklaştırılmasıdır.
Ayıklama adımının iyi yapılması diğer adımların etkili olması açısından çok önemlidir. İhtiyaç olmayan malzeme ve aletlerin ortadan kaldırılması ile iş güvenliğini sağlamak kolaylaşacak, verimlilik ve ürün kalitesi artacaktır.
Ayıklama adımı sayesinde çalışma ortamında boşta duran eşyaların, gereksiz ve düzensiz kabloların, zeminde duran el aletlerinin sağlık ve güvenlik riskleri oluşturması önlenebilir.
· Düzen (Seiton)
Sürekli ihtiyaç duyulan ekipman, demirbaş vb. malzemelerin bulunmasını ve kullanılmasını kolaylaştırmak amacıyla yapılan dizme, düzenleme ve tertip adımıdır. Bu adım her türlü alet, ekipman ve makineyi kapsar.
Bir çalışma ortamında düzen olmaması iş kaybı, aşırı yorulma, fazladan insan enerjisi kullanımı nedeniyle güvensiz bir çalışma ortamı oluşturur.
Ayrıca düzenleme adımında birbiri ile yan yana bulunması tehlikeli olan alet, makine ve malzemelerin de düzenlenmesini sağlar. Örneğin yanıcı ve yakıcı malzemelerin bir arada bulunması bu adım sayesinde önlenebilir.
· Temizlik (Seiso)
Çalışma alanlarında ve makinelerde çevre, üretim ve makine kaynaklı her türlü kirliliğin yok edilmesi ve korunmasıdır. Temizlik aynı zamanda duyu organlarımızla yapabileceğimiz bir kontroldür, oluşabilecek hataları önceden tespit etmemizi sağlar.
Çalışma ortamının temizlik olmaması çalışanların morali bozarak psikososyal yönden risk oluşturur. Ayrıca iş hijyenini olumsuz etkileyerek bulaşıcı veya kısa süreli sağlık problemlerine neden olur. İşyeri temizliği ve düzeni, diğer bir çok problemi daha başlamadan ortadan kaldıran bir etkendir.
· Standartlaştırma (Seiketsu)
Standartlaştırma adımı, diğer adımların sürekliliğinin sağlanması için oluşturulması gerekli standartlar, kontroller ve iyileştirmelerin bütünüdür.
Standartlaştırma ile her bir adımda yapılacak işler standart hale getirilerek kontrolü kolaylaşır ve hataların bulunması sağlanır. Standartlaştırma, diğer 3 adımın daha etkili yürütülmesini sağlar.
· Disiplin (Shitsuke)
Diğer adımların sürekliliğini sağlamak için standartlaştırma adımı ile belirlenen standart ve kuralların düzenli olarak kontrol edilmesidir. Disiplin adımı, diğer 4 adımı birbirine bağlayan çalışmadır.
Kural 8 : Bilgi Teknolojilerinin Kullanımı
Depo envanter yönetimini desteklemek için mevcut teknolojiler sürekli olarak gelişmekte ve sayıca artmaktadır. Küçük ölçekli işletmeler, büyük ölçekli işletmeler veya çok uluslu şirketlerin kullandıkları belirli yazılım uygulamaları vardır.
Depo envanter yönetimi yazılımı, her büyüklükteki depo için gereken temel bir teknolojidir. İyi bir sistem, deponuza giren envanteri kaydetmenizi ve deponuzdaki stok ve stok hareketlerinin konumunu yönetmenizi sağlar. Ayrıca siparişler ve toplama talimatları oluşturmak ve stok hareketlerini ve gönderileri kaydetmek için de kullanılabilir.
İyi bir depo envanter yönetim sisteminin diğer özellikleri ise:
- Sipariş yönetimi
- Üretim
- Satın alma, olarak sılanabilir.
Depo envanter yönetimi yazılımı kullanmanın en önemli yararı, verileri işleyerek daha sağlıklı bir şekilde karar alma ve en hızlı şekilde uygulamadır diyebiliriz.
ERKAN DÜZGÜN
Henüz yorum yapılmamış, sesinizi aşağıya ekleyin!